斜轨机床间隙:优化精度与效率的关键
斜轨机床是一种常用的数控机床,其具有较高的加工精度和效率。在实际应用中,机床间隙问题成为影响加工精度和效率的重要因素。本文将从随机8-20个方面,对斜轨机床间隙问题进行详细阐述,探讨优化精度与效率的关键。
斜轨机床间隙的概念与影响
斜轨机床间隙是指机床在加工过程中由于结构、传动等原因所产生的机械间隙。这种间隙会导致加工精度下降,影响加工质量和效率。具体影响包括加工误差的增大、表面质量的恶化以及加工效率的降低等。
斜轨机床间隙的原因
斜轨机床间隙的产生原因主要包括机床结构设计不合理、传动系统松动、磨损以及加工过程中的热变形等。例如,机床结构设计不合理会导致机械部件之间的间隙过大;传动系统松动会使得机床在加工过程中产生振动,进而影响加工精度。
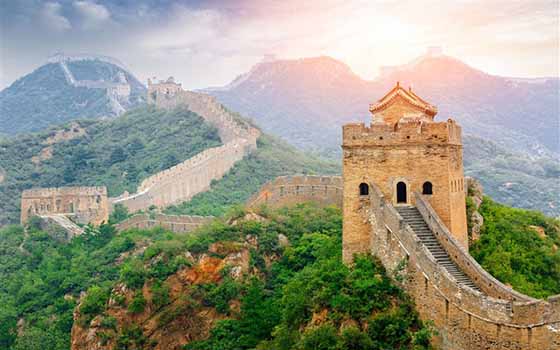
斜轨机床间隙的检测方法
为了准确检测斜轨机床的间隙,常用的方法包括激光干涉法、摄像测量法、振动分析法等。其中,激光干涉法是一种非接触式的测量方法,通过测量光束的干涉现象来获取间隙信息,具有高精度和高灵敏度的优点。
斜轨机床间隙的优化方法
针对斜轨机床间隙问题,可以采取多种优化方法。可以通过改进机床结构设计,减小机械间隙。可以加强传动系统的刚性,减小传动间隙。还可以采用补偿技术,通过控制系统对间隙进行自动补偿,提高加工精度。
斜轨机床间隙优化的关键技术
斜轨机床间隙优化的关键技术包括传动系统刚性优化、控制系统补偿算法以及加工工艺改进等。传动系统刚性优化可以通过选用高精度的传动部件、加强传动连接等方式来提高传动系统的刚性。控制系统补偿算法可以通过建立间隙模型,利用反馈控制技术对间隙进行自动补偿。加工工艺改进可以通过优化切削参数、改进刀具等方式来减小间隙对加工精度的影响。
斜轨机床间隙优化的实践案例
为了验证斜轨机床间隙优化的效果,可以进行实践案例的研究。例如,可以选择某个具体的斜轨机床,在不同优化方法的作用下进行加工试验,并对加工精度和效率进行评估。通过实践案例的研究,可以进一步验证斜轨机床间隙优化的可行性和有效性。
斜轨机床间隙问题是影响加工精度和效率的重要因素。通过优化机床结构设计、加强传动系统刚性以及采用补偿技术等方法,可以有效减小斜轨机床间隙,提高加工精度和效率。在实践中,需要结合具体的机床情况和加工要求,选择合适的优化方法,并通过实践案例的研究来验证优化效果。